The Digitization of Manufacturing: What To Expect in the Next 5 Years
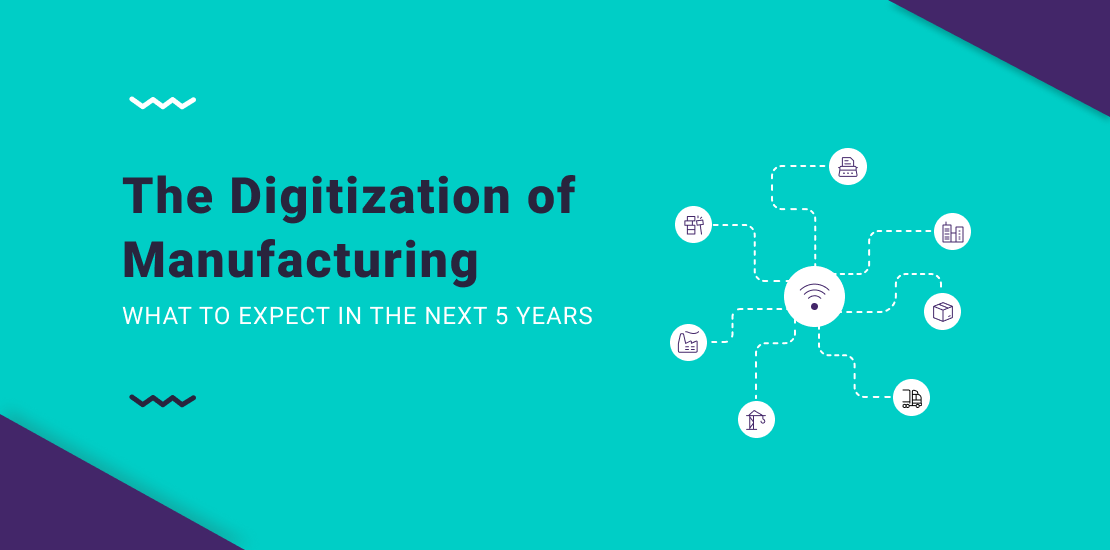
When people talk about the digitization of manufacturing, they often overlook the fact that most manufacturers have many digital components in place already.
Excel has replaced paper spreadsheets. 3D CAD drawings have replaced clay models. Engineers send drawings down to the floor via tablet, rather than running a book onto the shop floor. Most production lines contain a significant number of automated processes.
But what happens when you go further?
The examples above simply digitize existing processes. They don’t transform them into anything fundamentally different from what they were ten, twenty or even thirty years ago.
Now, thanks to pressure from consumers, new regulations and advances in technology, some manufacturers are changing the landscape of the manufacturing sector – digital transformation rather than just digitization. And, driven by a need to keep up with these new ‘digital champions’, other companies are fast following suit.
The new technologies that support this, which focus on interconnectivity, self-monitoring and increased automation are collectively known as ‘Industry 4.0’. You may have heard of some of them already, and may even have started to implement some of them into your processes.
As technology moves on, however, and more of it becomes accessible to a wider range of organizations, it’s essential to keep pushing digitization efforts forward.
Look ahead.
Keep an eye on on-the-horizon developments.
Have a plan for strategic technological investment and configure your processes to be able to adapt when the time is right.
Right now, manufacturing is at a turning point. Horizons have expanded more quickly and more extensively than anyone could have imagined even just ten years ago. Manufacturers that act decisively are likely to surge ahead of the competition.
Why is the Digitization of Manufacturing So Important, and Why Digitize Now?
At a basic level, digitization offers the following benefits
- Cost reduction: you complete the same process with fewer work hours and/or fewer staff
- Increased operational efficiency: you create more products in the same amount of time, with fewer wasted resources and man-hours.
- Reduction in human error: you reduce money lost to human mistakes, like operator error, damaged items or data loss.
These benefits aren’t new. Manufacturers have been using some form of automation for cost reduction and productivity gains since the dawn of the computer era, back in the 50s. So, what’s changed, and why is digitization more important than ever before for the sector?
It’s all about connectivity.
Well-planned strategic investment in connective Industrial Internet of Things (IIoT) technologies like machine-to-machine learning and predictive maintenance doesn’t just enhance the benefits above – it opens up a completely different way of operating for manufacturers.
Connected businesses produce and process far, far more data than humans could ever get their heads around themselves. Thanks to advances in connective AI technology, your machines can now collect, process and share that data with other machines without any human input whatsoever.
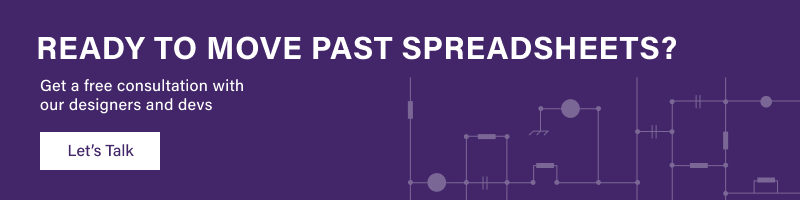
The Digitization of Manufacturing and The ‘Smart Factory’ Ideal
If your assets can store data about their own performance and communicate this with each other, they can start to optimize various processes without human involvement.
The ramifications of this are huge. If your products need to be made within particular environmental constraints, connected sensors could monitor this and adjust where necessary. Assets could use their own performance data to schedule their own maintenance, so that you spend less on replacement parts and they run at their best for longer. AI could run key factory processes, keeping retooling and resetting time to a minimum.
What if, instead of ironing out production faults, your engineers could leave this to the machines and spend their time on new product research and development?
What if you could reinvest savings made on machine maintenance into more strategically useful areas of your business, like attracting top talent or expanding into new markets?
Digitization gives you the freedom to reinvest human time and resources elsewhere.
A New Model of Operating for a Rapidly Changing World
As our collective focus turns towards sustainability, industrial digitization can assist dramatically in paving a greener future using connected technologies.
As concerns about our current linear approach to manufacturing (and the inefficiencies and waste that comes with it) grow, organizations have been looking for ways of implementing a more circular approach to product design and manufacturing. This includes business models like remanufacturing, leasing, asset management and incentivized return.
Investment in IIoT technologies, and the connectivity they offer in return, makes these significantly easier to achieve in two ways:
- Self-monitoring assets reduce breakdowns. This reduces waste caused by machine inefficiency and the need for replacement parts (and the extensive, often emission-heavy logistics operations needed to supply them).
- Sensors built into products themselves can increase efficiency and generate product data used for design improvements and flagging equipment repairs. You make fewer products, but you shift your business model to after-sales service and maintenance.
As well as being an inherently good thing to do, implementing more sustainable ways of operating will win you favor among increasingly green-conscious consumers – over half of all digital consumers now say that environmental concerns impact their purchasing decisions. One indirect benefit of the digitization of your manufacturing operations is that you can tap into this consumer trend. If your products are manufactured using cleaner processes whilst being mindful of resource use and recycling, that’s a major draw – use it to your advantage!
What Opportunities are there for the Digitization of Manufacturing Over the Next Five Years?
A perfectly connected, completely circular-economy enabling smart factory might not be achievable right this minute. But with IIoT technologies both developing rapidly and reaching a price point accessible to a wide range of manufacturers, it’s not as far away as you might expect.
So, if you want to start (or build on) digitizing your manufacturing operations, where’s best to focus to start seeing some more immediate benefits? A good percentage of your key processes are automated already – so what next?
If you’re looking to take things to the next level, here are the areas you should consider moving into.

Continued IIoT Investment/Development
To a large extent, some level of IoT adoption is now the norm for manufacturers.
PwC’s 2019 Internet of Things Survey suggests that 81% of manufacturers have already applied IoT to increase operational efficiency, and 68% plan to increase their investment over the next two years.
This means that if you’re working without any IoT implemented in your organization, it’s likely you’ll fall further behind over the next five years without some sort of investment as your competitors use the connectivity benefits to get ahead. If you’re in this position, now is the time to act.
And, if you do have some form of IoT already implemented into your organization – for example wearable technology for your warehouse staff or GPS sensors to track your logistics fleet or product shipments – there is now more scope for expansion than ever before.
You could consider:
- Predictive maintenance: the first step to realizing the ‘smart factory’ ideal is to invest in factory assets that can initiate their own maintenance once performance starts to wane. This could be by triggering an alert to an operator, or in more advanced cases auto-scheduling repairs and ordering their own replacement parts.
- Remote monitoring: enabling your assets with sensors means that you can monitor your machines’ (or in some cases your entire facility’s) performance without having to be there. Engineers can then adjust performance, which can save significant sums on staffing for remote facilities, or reduce the number of staff you need to run multiple facilities.
- IoT-enabled product design and development: adding sensors to your products allows your product designers to see how they perform in real time, so that they can implement targeted, iterative design improvements quicker than ever before.
- Robotics: robots free up your workforce from manual tasks so that you can redeploy staff in a more strategic capacity. It’s likely that you already have some form of robotics working in your factory or warehouse already. Now, thanks to wider availability, advances in AI technology and industry manufacturers specifically creating products to integrate with IoT-enabled robots, you can harness their productivity benefits even further.
Augmented Reality
Whilst a lot of Augmented Reality (AR) use cases like wearables and smart devices could be categorized under the IIoT section above, it’s worth spending a little more time exploring here.
That’s because AR is just about to hit the big time. Predictions suggest an eye-watering expansion of the market to $198 billion in 2025, from a base of $1.8 billion in 2018
AR places computer-generated objects and environments over real-world settings through use of video technology. You may have seen how this works in a couple of non-manufacturing settings already:
- With trends towards online shopping growing thanks in part to the Covid-19 pandemic, retailers in particular are using AR to help customers come to a purchase decision. IKEA’s AR app helps customers visualize a piece of furniture in their home setting by linking with their device’s video camera.
- AR is used in increasing numbers of video games for an immersive experience, such as Pokemon Go.
Organizations are fast waking up to the opportunities AR offers in a manufacturing setting. The classic example here is using smart lenses to speed up logistics processes – your warehouse staff can use them to receive and pick orders more quickly using onscreen maps and directions. In large warehouses, this saves significant time in trips to a specific station each time to log completed orders and pick up new ones, so you process more orders each day.
Now, however, cutting-edge manufacturers are seeing its potential far beyond the supply chain.
Product Design and Development
Consider how much more effectively you can design new products using CAD than using traditional models. AR ramps those productivity benefits up even further, allowing designers to iteratively test multiple variations of a product in an augmented-reality environment rather than relying on physical prototypes.
This means that:
- You can test your designs at a vastly reduced cost because you don’t need to invest in materials to build early-stage physical prototypes.
- You can explore how a design would behave in real life using an AR environment. Previously, it has been extremely difficult for designers to determine how a design will behave without constructing a prototype. Now, designers can experiment with products in simulated realities to improve the functionality of your first physical prototypes.
If you combine AR with advances in 3D printing, you can design, create and test workable physical prototypes faster and cheaper than ever before – a useful edge to have if you want the ability to scale quickly and beat competitors to market.
Assembly
To create a particularly complex product, it’s likely that your technicians will have access to diagrams, schematics and laptops. This means that, in order to get the information they need to complete the job, they have to look away constantly to refer back to these instructions.
Why not make it easier for them by removing this need, freeing up hands and providing exactly the right instructions needed at a certain point in time?
That’s exactly what aircraft manufacturing heavyweight Boeing has done for its wiring technicians. Through a combination of Google Glass and Skylight, Boeing techs receive instructions exactly when they need them via their glasses, and can use voice commands to bring up on-screen how-tos. Meanwhile head-tracking technology and Google Glass cameras help identify and confirm the wiring inventory.
The result? A massive 25% reduction in wiring time and an error rate of virtually zero – an outcome that could place Boeing considerably ahead of comparable companies if they roll out the practice company wide.